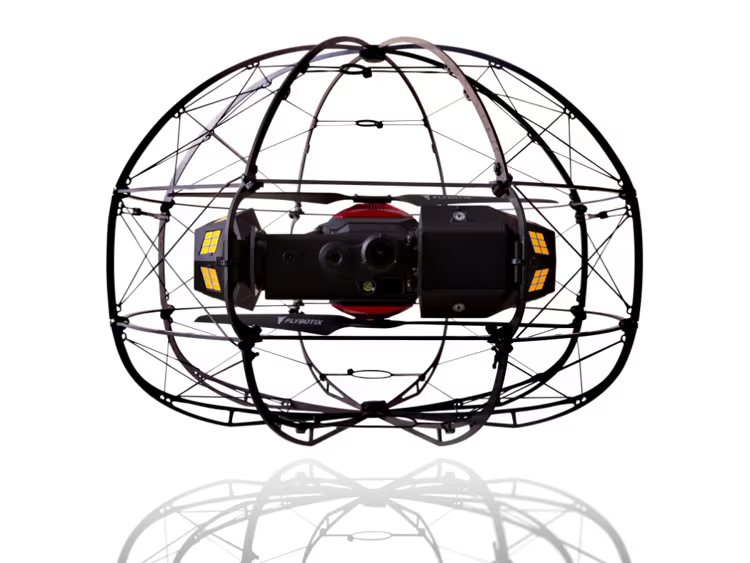
Introduction
Drones have revolutionised the way inspections are conducted in hazardous and hard-to-reach areas, such as sewers, penstocks, tanks, and chimneys.
These environments pose significant risks for human inspectors. The advent of drones equipped for harsh conditions has enabled access to such sites while minimising human risk.
This case study focuses on the ASIO X drone, emphasising its extended flight time feature, which greatly enhances its operational efficiency compared to other drones with limited battery capacity.
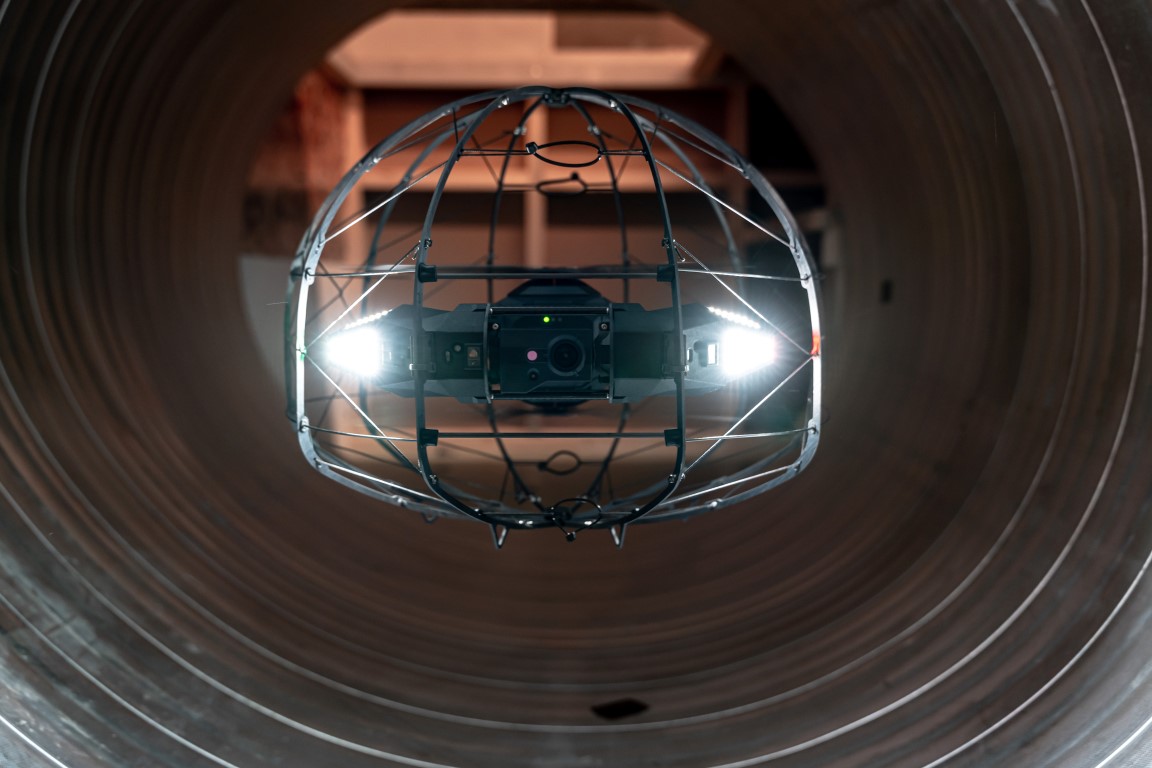
Challenge
Internal inspection drones, while capable of hovering in place to collect detailed data, often suffer from limited flight times due to the high energy demands of maintaining thrust.
This limitation restricts the range and duration of inspections they can perform. Factors such as lighting usage and environmental conditions like wind and air density can further reduce effective flight time.
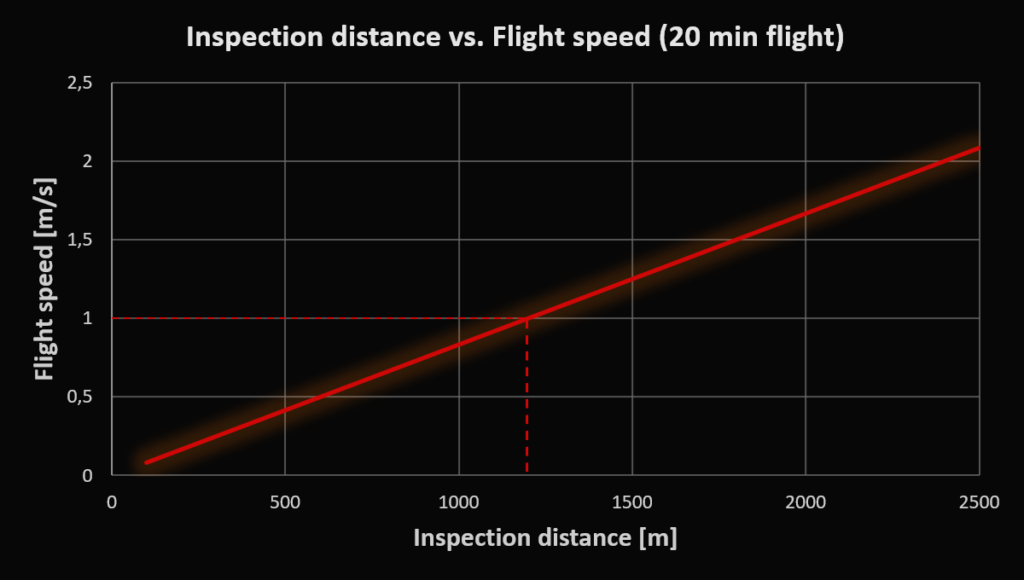
Confined Space Drones Flight Time
Confined space drones are specialised unmanned aerial vehicles (UAVs) designed to access and navigate areas that are otherwise difficult or dangerous for humans, such as sewers, tanks, tunnels, and other tight spaces.
These drones are engineered to collect critical data using various sensors, including high-definition cameras, LiDAR, thermal imaging and gas detection. However, their compact size and the need for multiple data outputs present a significant challenge, creating a catch-22 situation.
The primary issue lies in the power requirements and battery limitations of these drones. Most confined space drones are powered by lithium polymer (LiPo) batteries, which offer a finite amount of energy for flight and data collection.
The more power-intensive the drone’s operations—such as maintaining stable flight, maneuvering in tight spaces, and operating multiple sensors simultaneously—the faster the battery drains. This results in reduced flight times and, consequently, the need for frequent battery changes.
Adding more data-gathering devices, such as thermal sensors, LiDAR, and NDT equipment, exacerbates the problem. Each additional sensor consumes more power, further decreasing the available flight time.
For instance, during a sewer inspection, where the drone is required to fly through long and complex passages, the limited battery life becomes a critical constraint. Even with multiple battery changes, the drone’s range can be severely restricted, sometimes to as little as 150-300 meters, which is often insufficient for comprehensive inspections.
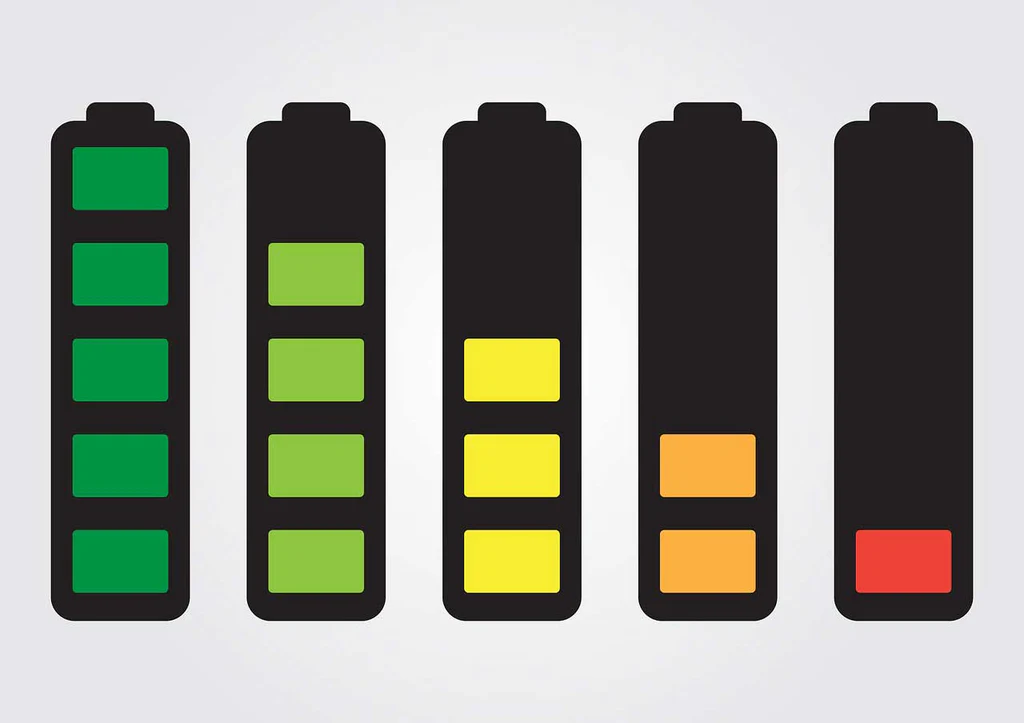
Additional or larger batteries?
An obvious solution to extend flight time is to equip the drone with larger batteries. However, this approach introduces additional problems. Larger batteries can increase the drone’s overall size and weight, making it more challenging to access and maneuver within confined spaces.
The added weight also puts a greater demand on the motors, which in turn increases power consumption and further reduces the battery’s performance. This can lead to a situation where the increase in battery capacity is offset by the additional power required to lift the heavier payload, resulting in little to no improvement in overall flight time.
Moreover, the increased size of the drone with larger batteries may prevent it from accessing the very confined spaces it was designed to inspect. The delicate balance between size, weight, and power becomes a critical factor, and any deviation can severely impact the drone’s ability to perform its intended tasks effectively.
In an attempt to maximize coverage within the limited flight time, drone pilots may fly more aggressively or erratically. This can lead to less stable flight paths and potentially compromised data quality, as the sensors may not be able to collect accurate or consistent readings during rapid or abrupt movements.
The result is a paradox: to gather the required data, the drone needs to carry multiple sensors, which in turn reduces its operational time and range, ultimately defeating the purpose of the inspection.
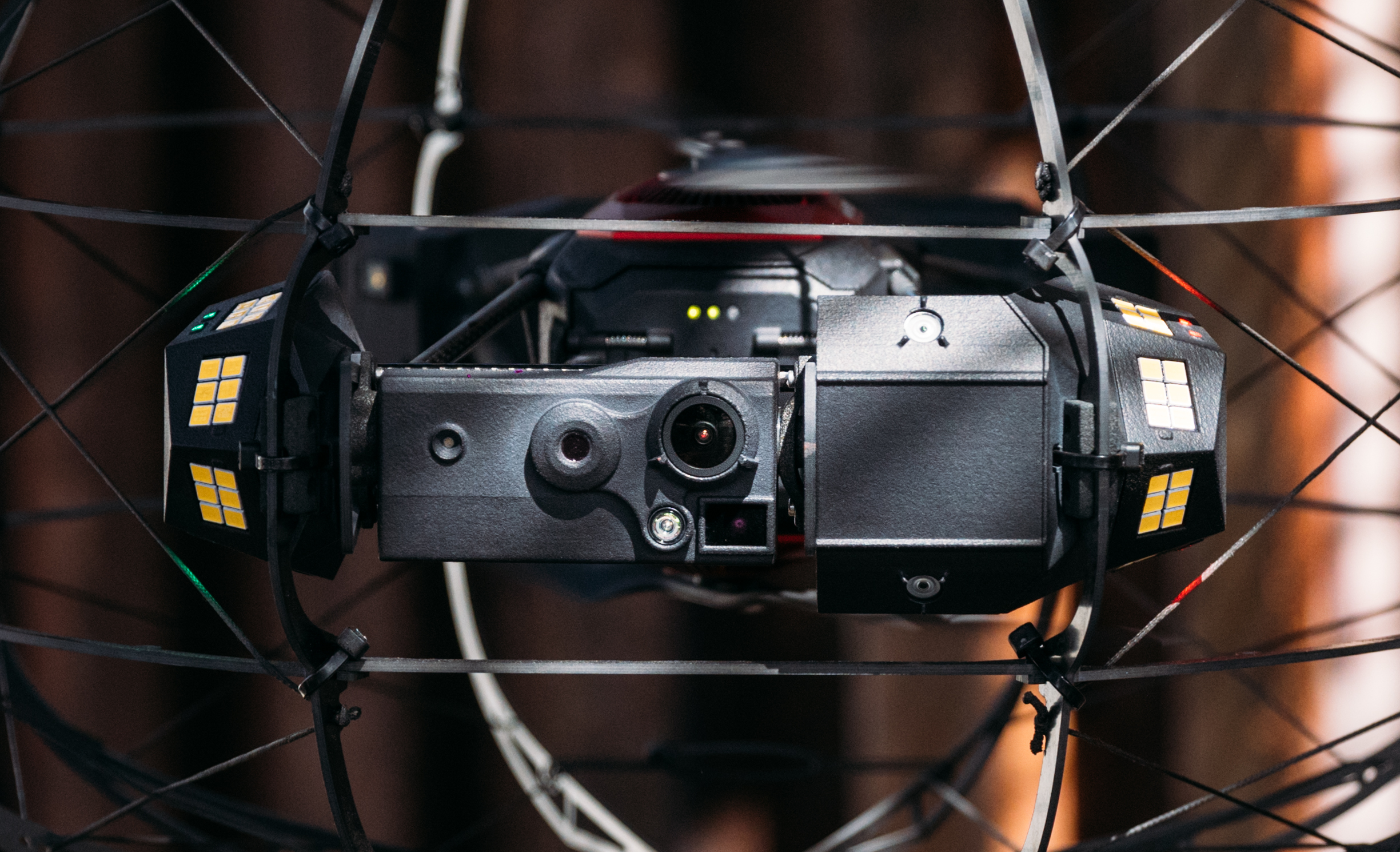
Catch-22
This catch-22 situation underscores the need for innovative solutions, such as improved battery technology, more efficient power management, or even alternative power sources that can extend flight times without compromising the drone’s compact size and functionality.
As confined space drone technology evolves, addressing this challenge will be critical to enhancing the effectiveness of these UAVs in industrial inspections and other applications.
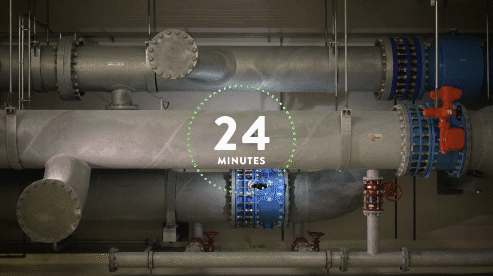
Flybotix Asio
The ASIO drone is designed with a coaxial system that optimises energy use, allowing for flight times of up to 24 minutes.
This extended capability is critical for conducting thorough inspections over large distances or in complex environments without the need for frequent recharging or battery swaps.
With a 20-minute flight capability, the ASIO drone can cover distances up to 1000 meters. This is significant for inspections of lengthy penstocks, where access points may be widely spaced.
For instance, a recent inspection of a 1200m penstock was completed in just over 15 minutes, demonstrating the drone’s ability to cover extensive areas efficiently.
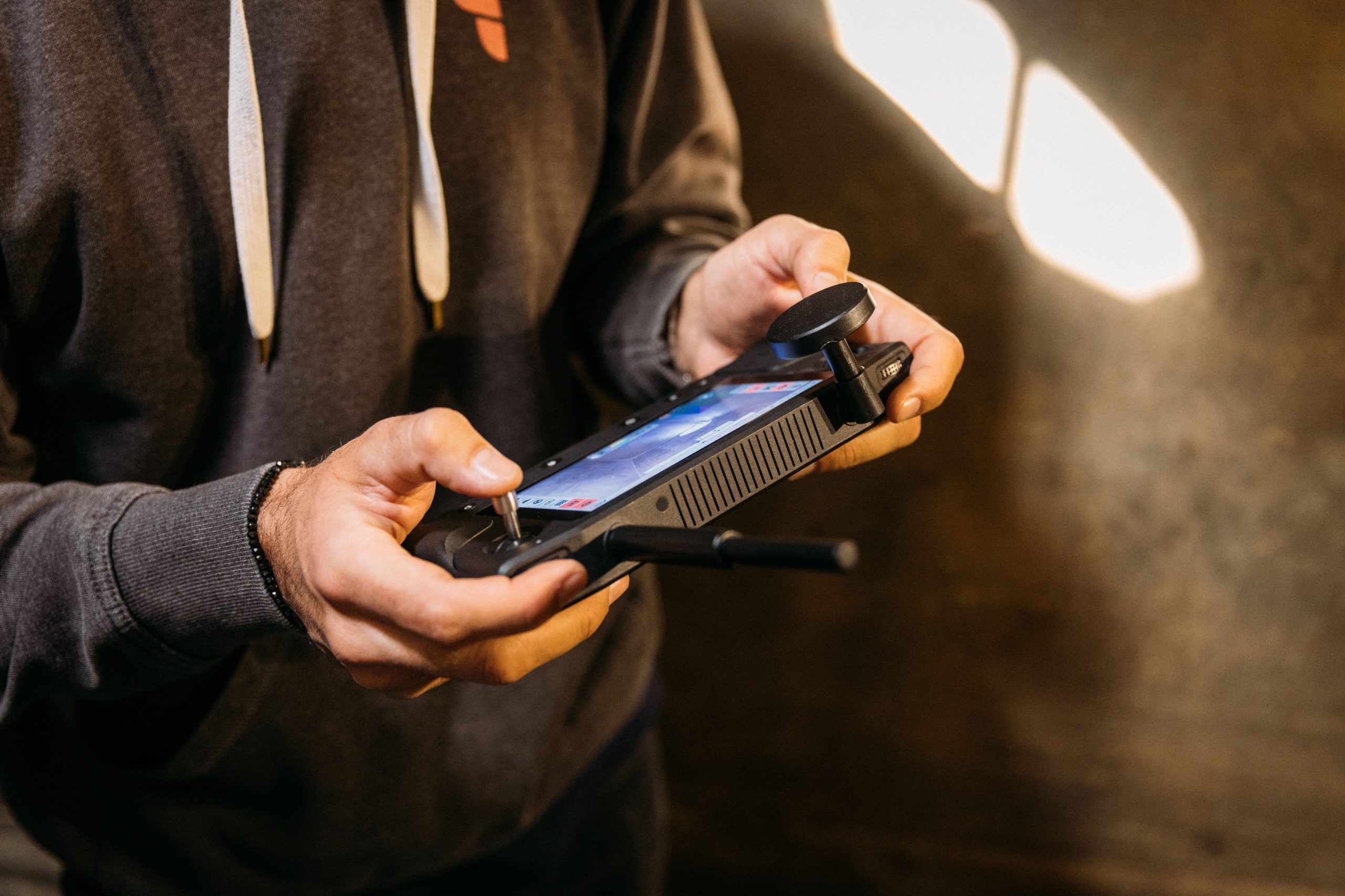
Pilot and Inspector Advantages:
Pilot and Inspector Advantages:
The extended flight time reduces the frequency of landings and battery changes, lessening physical strain and operational downtime. Pilots can manage inspections with less stress and higher concentration, leading to fewer errors and more precise data collection. Inspections at slower speeds allow for meticulous examination of structural integrity, potential blockages, or damage within the penstock.
Adaptability to Inspection Needs:
Depending on the mission specifics—distance, complexity of the environment, and data precision required—the drone’s flight speed can vary.
For shorter distances (up to 300 meters), the drone can fly slower, focusing on detailed data collection. For longer stretches, even at speeds up to 1 m/s in visual lock-assisted mode, the drone maintains effective data accuracy and flight stability.