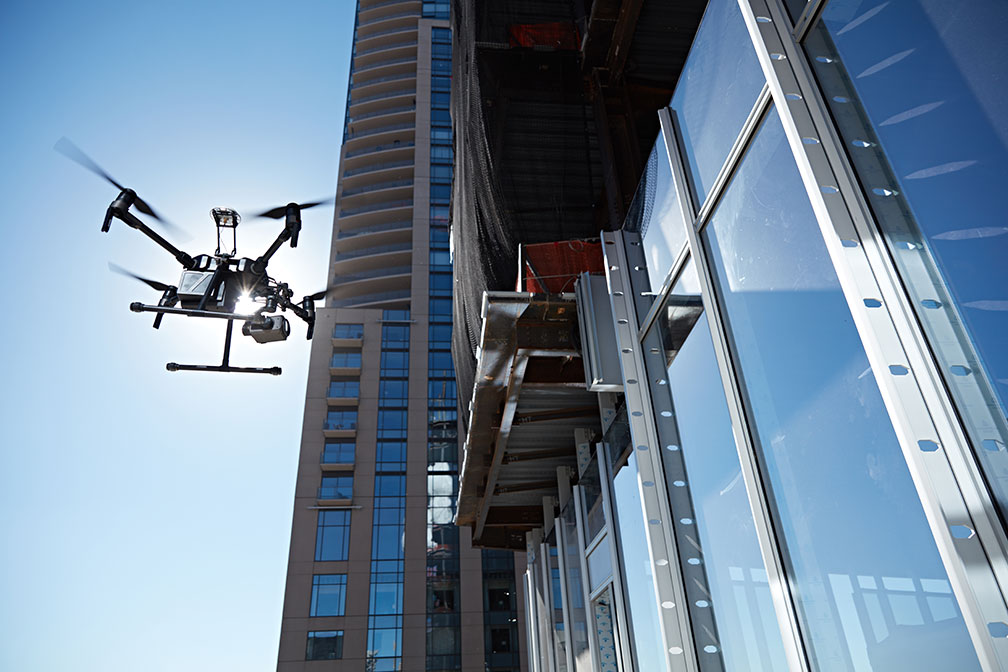
Overview
Iprosurv was commissioned to inspect a 15-storey tower block in Leeds due to a critical safety issue. Large External Wall Insulation (EWI) panels, installed just five years prior, had begun cracking and detaching from the building’s facade.
Weighing approximately 25 kilos, these panels were falling from heights of up to 47.5 meters, posing a severe danger to residents and the public.
The local housing association and authority required a quick, cost-effective inspection method to triage and prioritise necessary repairs not just for this building, but for others in their portfolio.
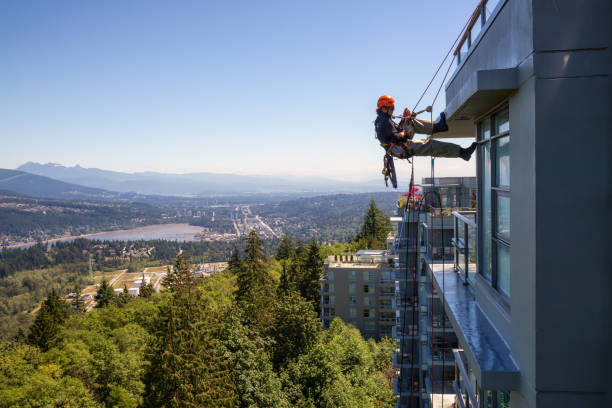
Challanges
The primary challenges included:
- Safety Risks: Large EWI panels were cracking and becoming dislodged, falling to the ground from significant heights.
- Time Sensitivity: Traditional methods, such as scaffolding and rope access, involved lead times of up to two months and extensive logistics.
- Cost-Effectiveness: The housing association needed a solution that was not only faster but more affordable than traditional inspection methods.
- Detailed Coverage: Ensuring every aspect of the building’s exterior was thoroughly inspected to assess the extent of the damage.
- Workmanship Concerns: Given that the cladding had been installed only five years prior, there were questions about the quality of installation workmanship, which needed to be addressed in the inspection report.
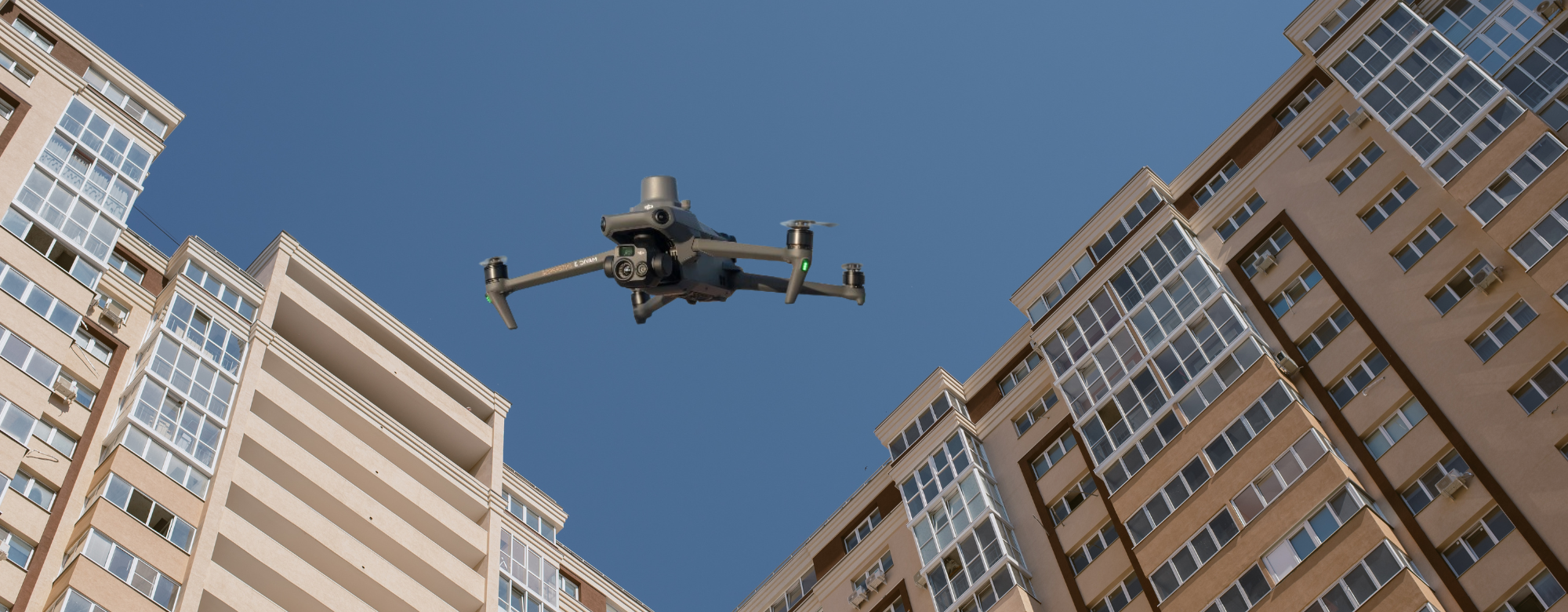
Implementation of Drone Technology
Iprosurv proposed using drones for a detailed survey of the building. The drone inspection took thousands of high-resolution images of the building’s exterior, covering every angle.
This approach allowed for comprehensive coverage, something unachievable through traditional methods like scaffolding, rope access, or elevated platforms.
The drones were operated by experienced pilots, ensuring that all risk areas were carefully documented.
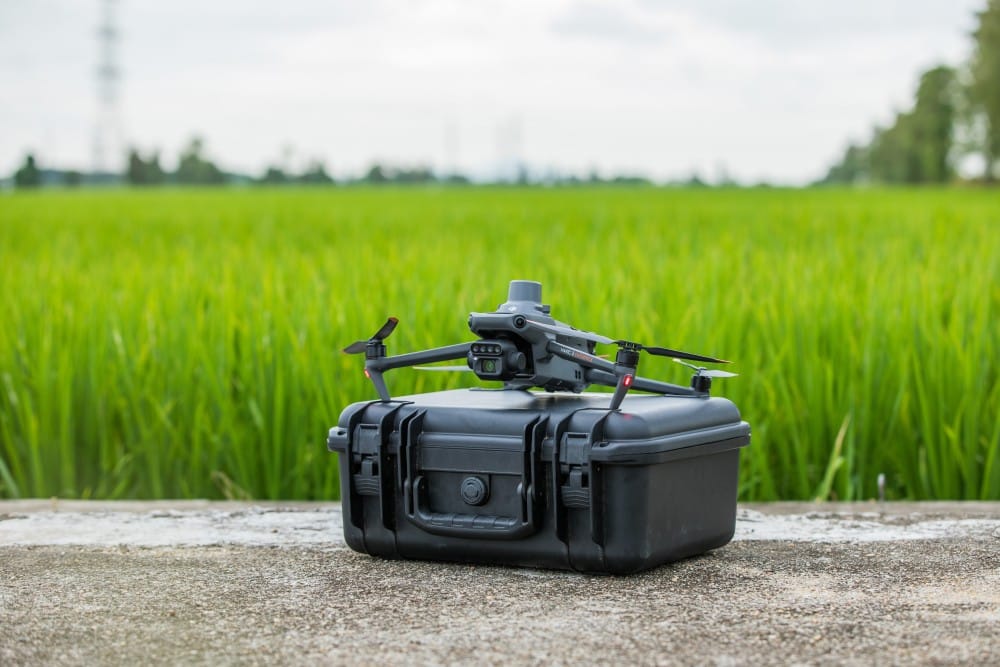
Advantages of Drones in This Case Study
Using drones provided significant advantages:
- Speed: The entire process, including planning, on-site data collection, and reporting, was completed within 72 hours. Traditional methods would have taken weeks or even months.
- Cost Efficiency: Drones eliminated the need for expensive scaffolding and rope access while delivering superior results.
- Comprehensive Coverage: The drones captured high-definition images of the entire facade, including hard-to-reach areas, ensuring no defect went unnoticed.
- Non-Intrusive: The inspection process was non-intrusive, allowing residents to remain in their homes during the survey.
Software
After collecting the drone images, Iprosurv used advanced software to process and compile the data into a detailed 3D interactive model of the tower block.
This model allowed for desktop investigation, enabling stakeholders to explore every aspect of the building in detail.
The software also facilitated the generation of a white-labelled report, which detailed all defects, their locations, and the extent of the damage.
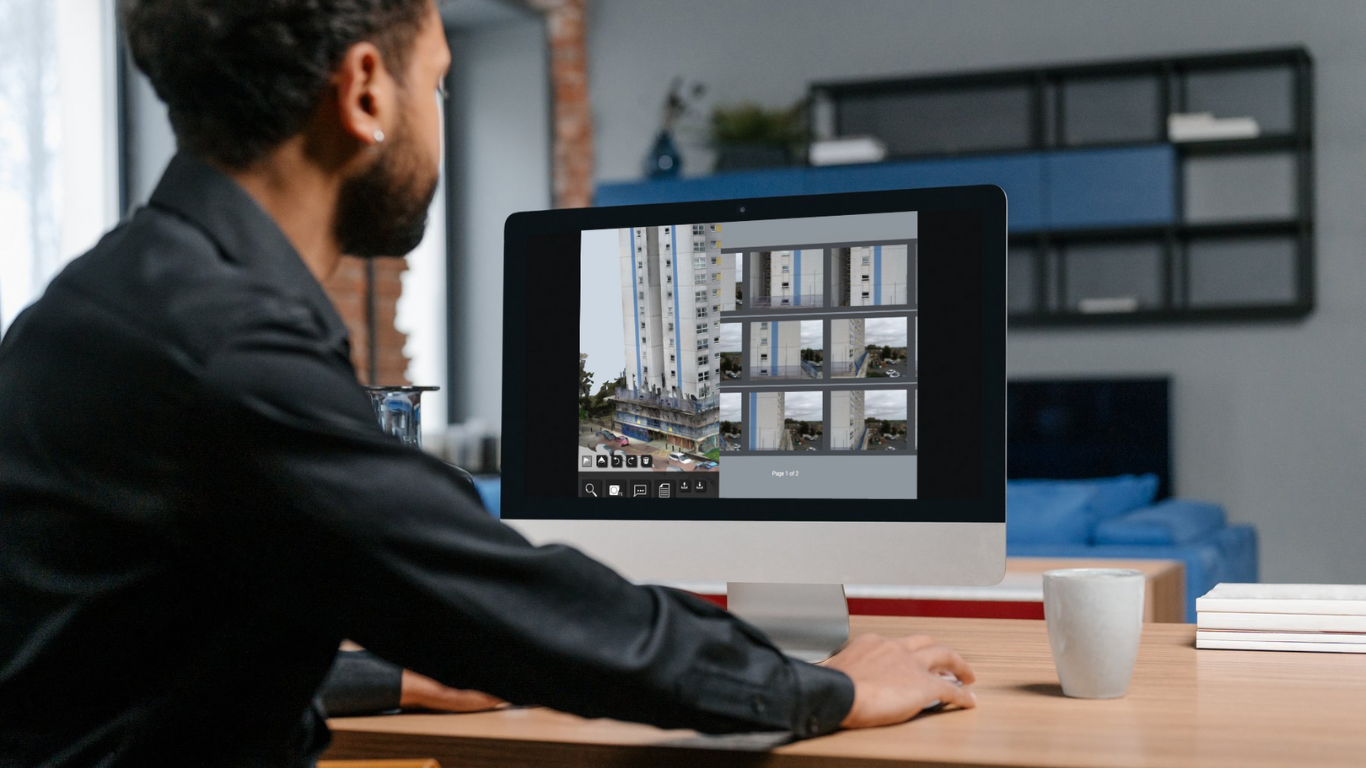
Data Processing
The processing of thousands of images took just one day, thanks to Iprosurv’s cutting-edge technology. The data was converted into a comprehensive, detailed 3D model of the tower block, which could be analysed remotely by the housing association and local authorities.
Additionally, the software was equipped with AI-powered crack detection capabilities, which automated the identification of cracks and structural weaknesses across the facade.
This feature provided an even more thorough and efficient analysis by flagging potential issues that might be missed in manual inspections.
This AI-driven functionality allowed the housing association to detect and assess risks faster and more accurately, ensuring all defects were noted for repair prioritization.
The software’s user-friendly interface allowed for easy navigation and defect identification, speeding up decision-making processes and enabling better-informed repair strategies.