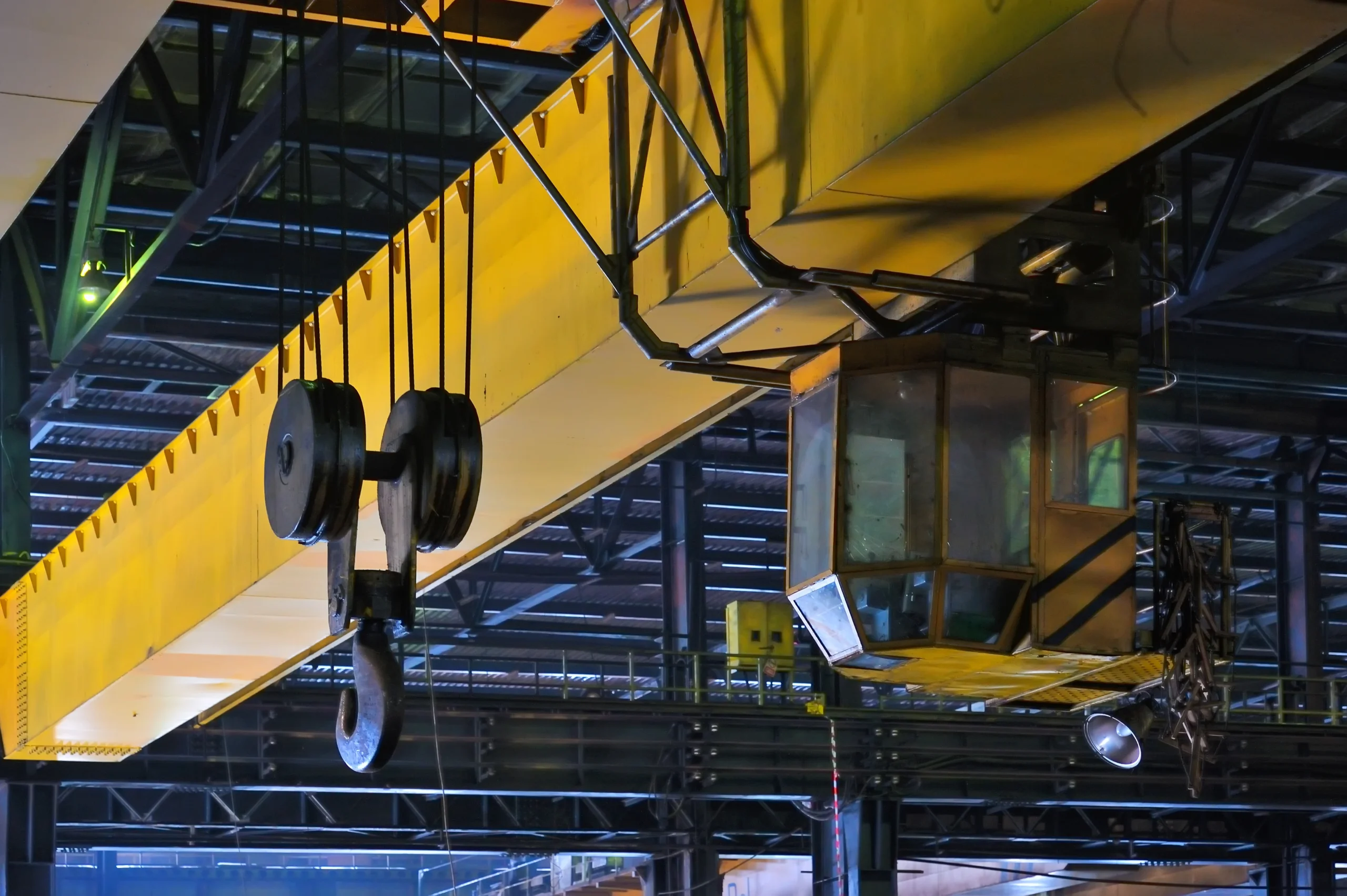
Introduction
In the utilities industry, the maintenance and inspection of assets are critical for operational efficiency and safety. However, traditional inspection methods often involve significant downtime, high costs, and logistical challenges. Iprosurv, a leader in drone technology, has developed innovative drone solutions that transform statutory LOLER inspections, particularly evident in our collaboration with Thames Water. This case study explores how drones are revolutionising asset inspections, reducing downtime, and increasing efficiency within the utilities sector.
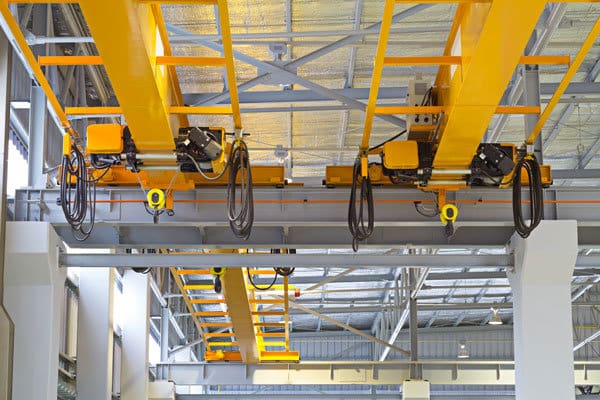
Challenge
Traditional methods of asset inspection in the utilities industry, such as the use of scaffolding or manual access, are not only costly but also time-consuming. These methods typically require shutting down facilities to ensure safety, which results in assets being out of commission for extended periods. This necessary downtime leads to increased costs and reduced overall efficiency, impacting service delivery and operational continuity. The challenge is to find a more efficient, cost-effective, and less disruptive method for conducting these essential inspections.
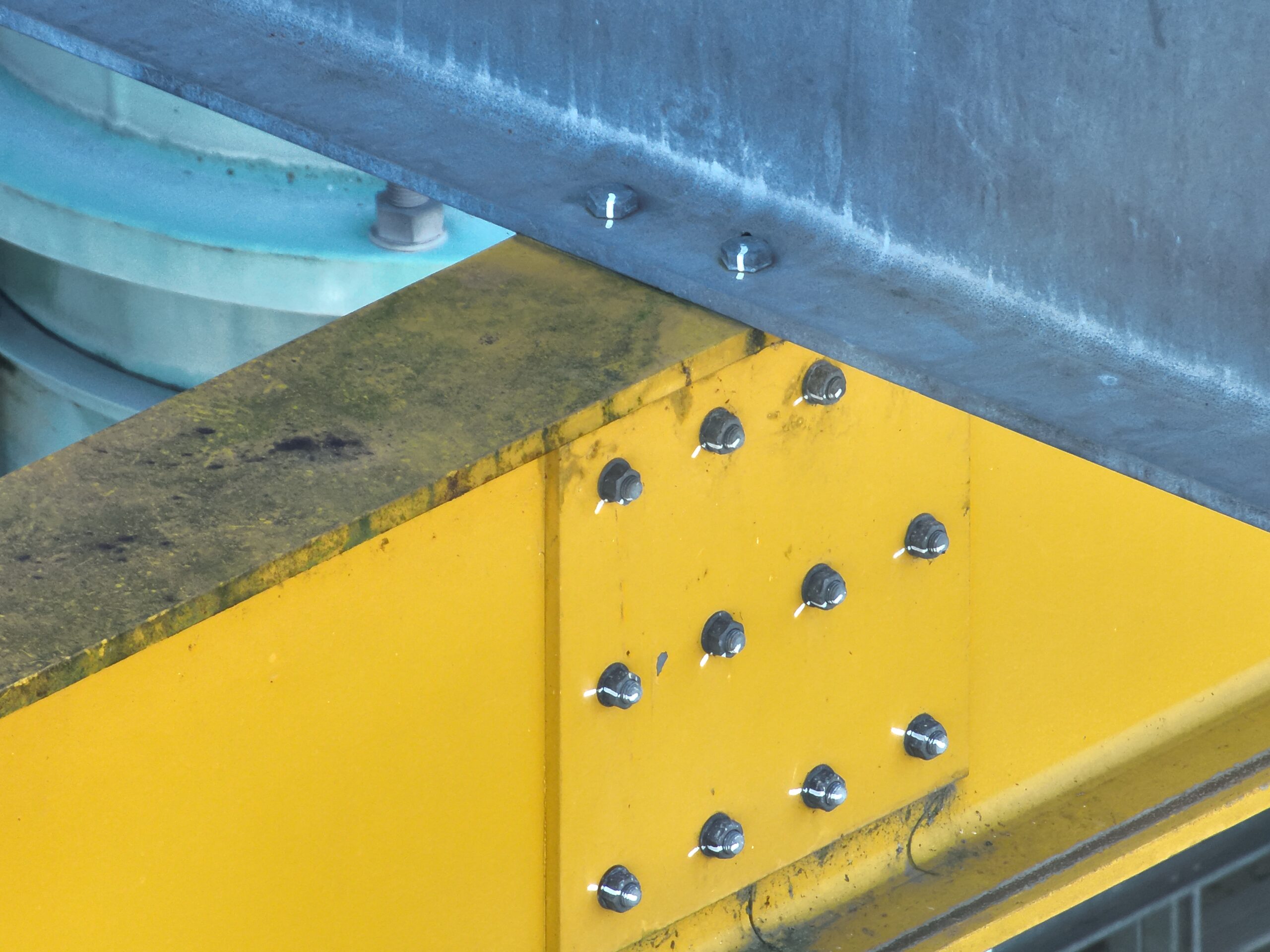
Implementation of Drone Technology
In response to these challenges, Iprosurv has introduced advanced drone technology to perform asset inspections. Our drones are equipped to operate in GPS-restricted environments, allowing them to navigate close to and around complex structures, like those found in water treatment facilities. At Thames Water, drones have been integrated into a five-year inspection rotation plan, enhancing the traditional inspection regime.
The initial year involves a physical inspection to establish a baseline and implement witness marks on critical components, such as bolts. In subsequent years (2, 3, and 4), drones are used to inspect these witness marks for any signs of movement or degradation, eliminating the need for physical access. The cycle repeats with a physical inspection in the fifth year, ensuring thorough oversight while maximising operational uptime.
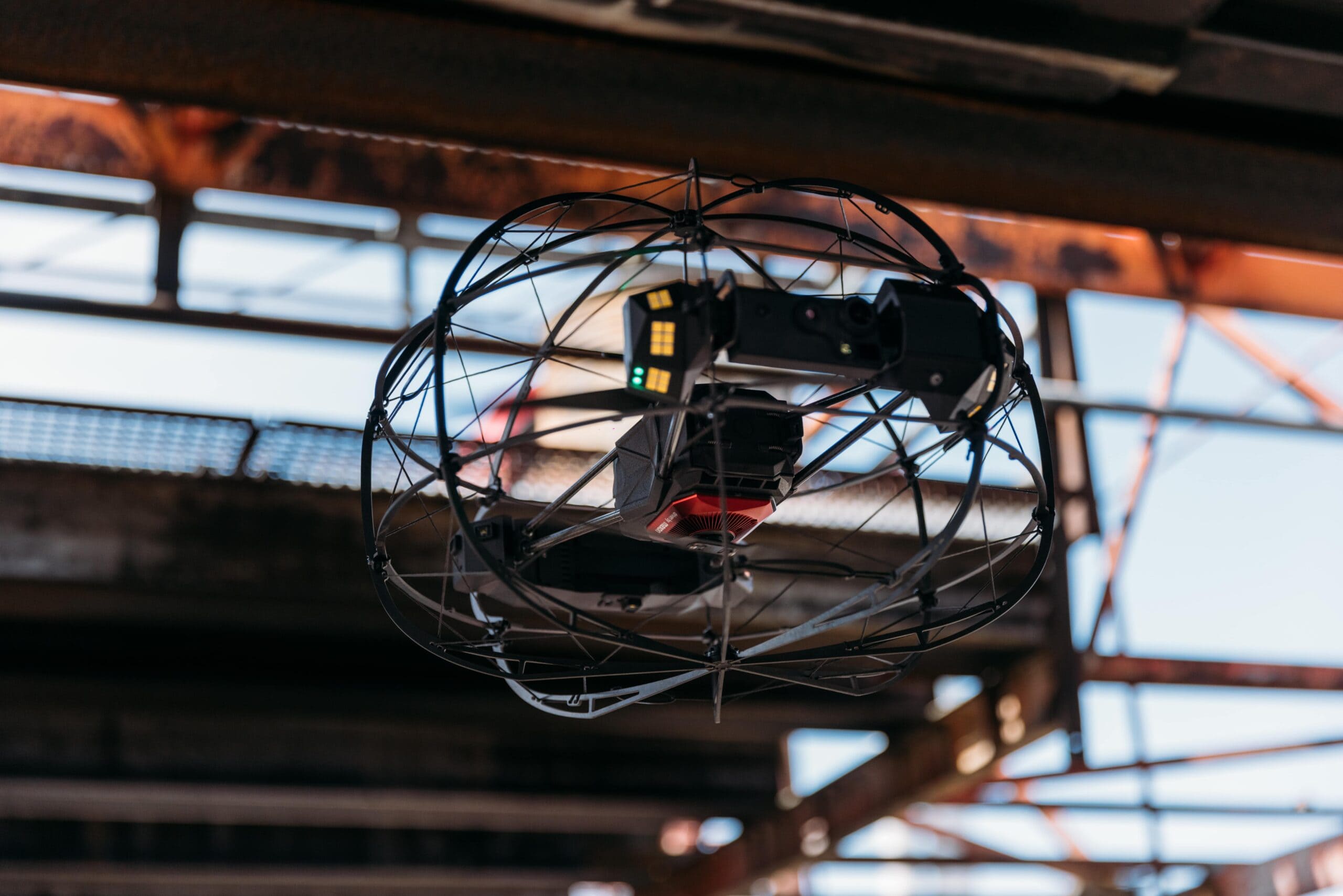
Advantages
The adoption of drone technology for LOLER inspections offers multiple advantages:
- Cost Efficiency: Drones reduce the need for expensive scaffolding and manual labour, significantly cutting down the costs associated with traditional inspection methods.
- Speed: Drone inspections are completed much faster than manual inspections. This rapid deployment capability means less planning is required, and assets spend minimal time out of service.
- Simplicity and Repeatability: Drone operations are easy to standardise and repeat, ensuring consistent and reliable inspections that can be easily documented and reviewed.
- Reduced Planning and Time to Site: Drones can be deployed quickly with minimal setup time, which is crucial for emergency inspections or in response to unexpected maintenance issues.
- Health and Safety Benefits: Drones significantly reduce the need for human presence in hazardous and elevated environments, minimising the risk of accidents and promoting safer workplace conditions.
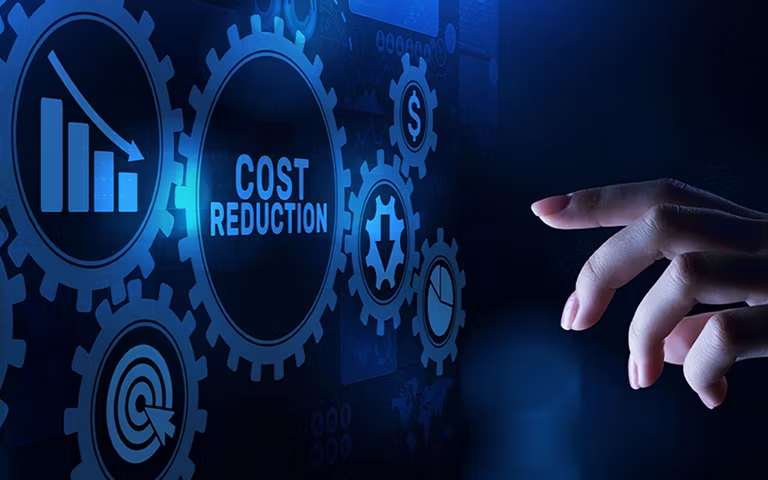
Cost Savings on This Project
Certainly, here’s a paragraph with bullets about the cost savings for using Flybotix Asio X drones in statutory and LOLER inspections for internal gantry cranes:
Utilising Flybotix Asio X drones for statutory and LOLER inspections of internal gantry cranes presents substantial cost savings compared to traditional methods such as scaffolding and elevated platforms. Here are the key financial benefits:
- Cost Efficiency: The use of drones can lead to savings of approximately 60% per inspection, equating to around £25,000 in cost reductions.
- Asset Downtime: Traditional methods typically require 2-3 weeks of asset downtime, whereas drone inspections can reduce this to just one day.
- Reduced Booking Lead Time: Faster setup and deployment times of drones decrease the booking lead times for inspections.
- Equipment Hire Savings: Eliminates the need for costly hire of scaffolding and elevated platforms, further reducing overall expenses.
By integrating Flybotix Asio X drones into the inspection process, businesses can achieve significant financial and operational efficiencies.